Last week, the PredictLeads changed Google chats and company data to glamour, secrets, and suspense. Our destination? A one-of-a-kind immersive mystery game set in the roaring 1920s.
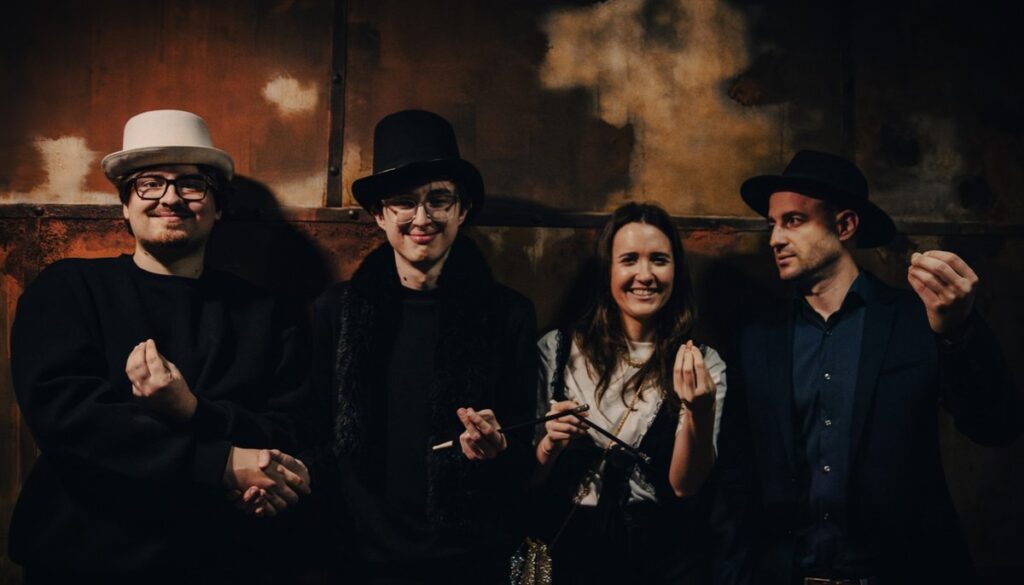
Dressed in our finest vintage attire, we joined forces (and in some cases, formed rivalries) to solve a high-stakes Gatsby-themed that brought out the detective (and the actor) in all of us.
Reimagining Team Bonding in the Style of The Great Gatsby
As part of our ongoing commitment to fostering strong team culture, we wanted to do something more and were looking for an experience that was collaborative, interactive, and completely unexpected.
Each of us was assigned a character – from wealthy elites and ambitious entrepreneurs to struggling artists, cunning politicians, and even a few shady underworld figures. With roles in hand and costumes to match, we were immersed in a glamorous, high-stakes environment filled with intrigue, hidden agendas, and unexpected twists.
A Night of Suspicion, Alliances, and Twists
The game kicked off with whispered theories and hushed conversations. Who could we trust? Who had something to hide? Working in small groups, we pieced together clues, questioned timelines, and uncovered motives.
And just when we thought we had it figured out – boom. A final twist turned everything upside down. We won’t spoil the ending, but let’s just say that more than one person is still debating whether the artist was secretly behind it all.
Dressing the Part: Vintage Glam Meets Office Culture
What made the evening even more memorable was the team’s commitment to the theme. Feathers, fedoras, flapper dresses, suspenders, red lips, and sparkling accessories transformed our crew into characters straight out of a F. Scott Fitzgerald novel.
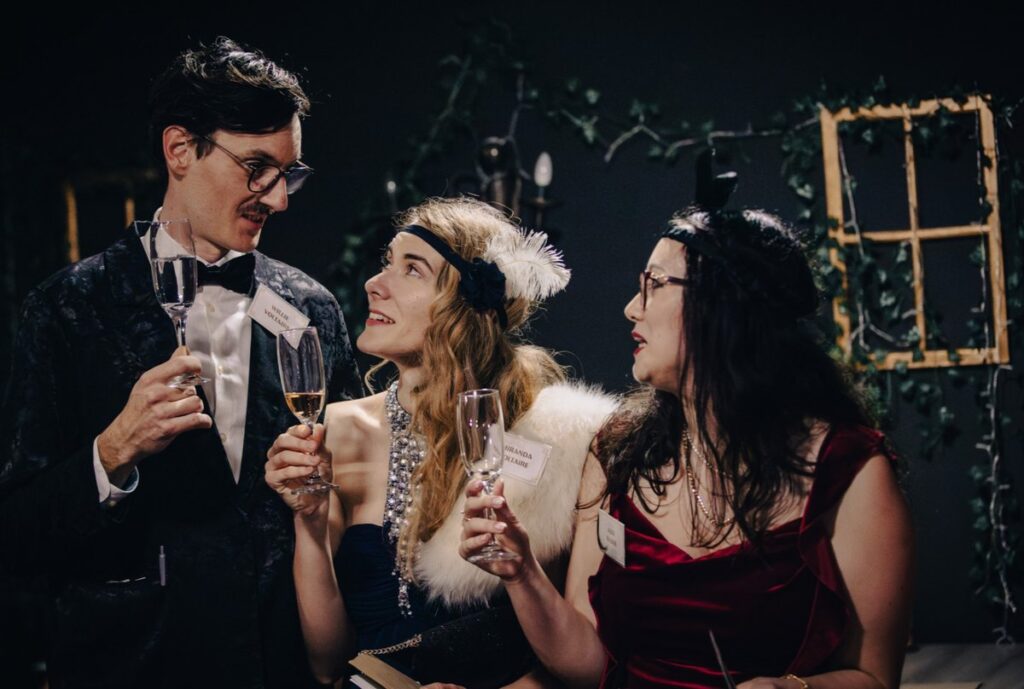
For many of us, it was the first time we’d seen each other outside our usual roles. People embraced their alter egos, delivered dramatic monologues, and even discovered unexpected talents for improvisation and persuasion.
Unique Team Events Matter
At PredictLeads, we know that team-building activities aren’t just about having fun, but they’re about building trust, encouraging creative thinking, and strengthening our collaboration across roles and departments.
This 1920s mystery night reminded us that behind every line of code and every data insight is a team of curious, resourceful, and creative people. When we step outside our usual routines (even just for a night) we return more connected, more energized, and more in sync.
Planning a Team Building Event? Try a Mystery Game
If your company is looking for a unique corporate event idea, we can’t recommend immersive mystery games highly enough. They combine teamwork, communication, and problem-solving > all wrapped in an experience that people won’t forget.
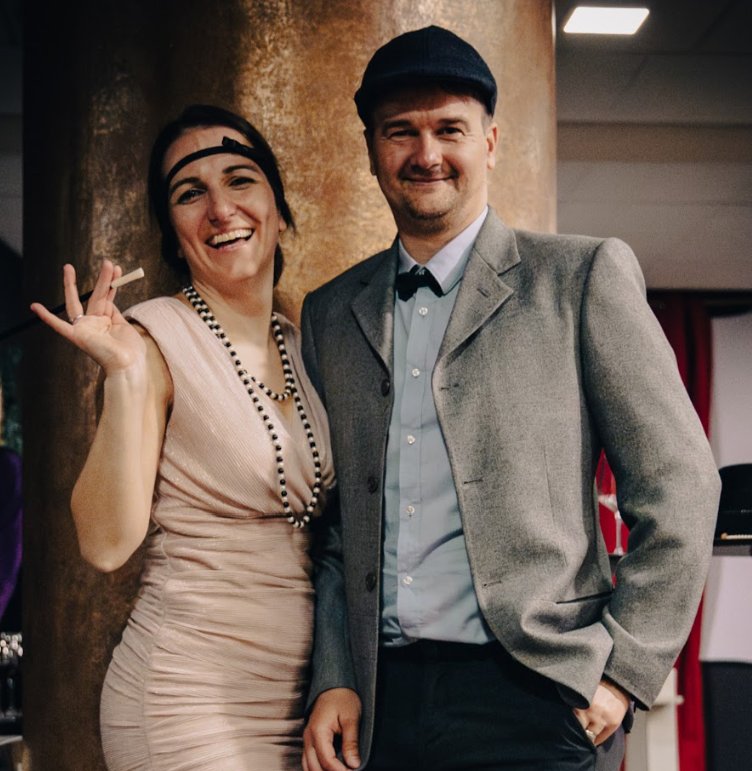
We came for the mystery. We left with stronger connections, unforgettable memories, and a renewed appreciation for the people behind the PredictLeads brand.
Until next time,
The PredictLeads Team 💜